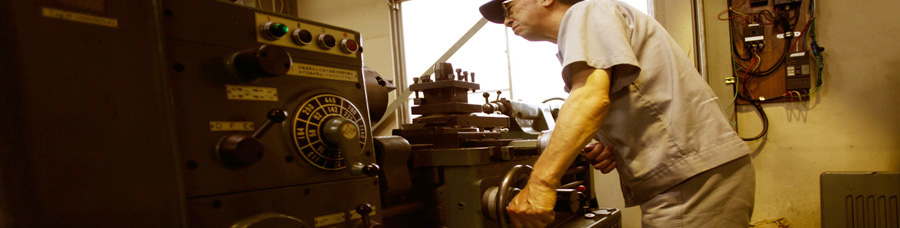
Technologies
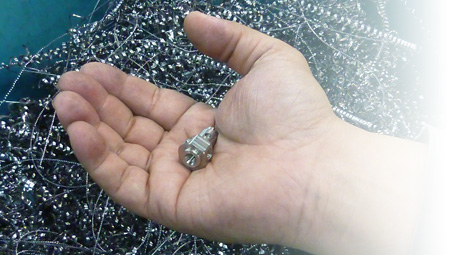
The predecessor of Mikami Co., Ltd., is Mikami Seiki, which was established on Jun. 1, 1967. Since the Mikami Seiki days, we have maintained high-standard part processing technologies in lathe machining enabled by experienced and strengthened craftsmanship, and we are proud of our substantial contribution to the manufacturing industries in Japan.
We inherit this craftsmanship as the tradition of Mikami’s technical capability to satisfy every request from our customers, even after introducing the latest processing machines.
We inherit this craftsmanship as the tradition of Mikami’s technical capability to satisfy every request from our customers, even after introducing the latest processing machines.
Technologies ▶ Mirror Surface Processing
Our cutting technologies enable mirror surface processing of 0.8s or less in cutting process.
Polishing is not required at post-process.
Polishing is not required at post-process.
Technologies ▶ Thin-film Processing
Generally, Thin films are welded to the body in thin-film processing, which is needed for the manufacturing of sensors. Our technologies, however, allow machining of thin films up to 0.1 mm in thickness in the single process of cutting. This processing technology is superior in terms of both accuracy and strength.
Technologies ▶ Restructuring of Process
Restructuring of the process is enabled by building unique programs through detailed examination of the processes using the know-how accumulated over many years.
This eliminates variations in accuracy and enables cost savings.
This eliminates variations in accuracy and enables cost savings.
(1)Cam pipe cut in one process to maintain high accuracy
(2)Realization of mass-production using materials flexible enough to change shapes from the pressure of female fingers
(3)Male screw: at the peak of its screw thread, another groove was machined by a lathe.
(2)Realization of mass-production using materials flexible enough to change shapes from the pressure of female fingers
(3)Male screw: at the peak of its screw thread, another groove was machined by a lathe.